Pulleys
Engineered, Optimised and Manufactured to the Highest Quality Standards
Manufactured by Fenner Conveyors and custom designed to your individual requirements using sophisticated computer modelling based on the steady state and transient loads for the conveyor. Fenner Conveyors is unique in our ability to offer such an extensive range of customisation options – delivering you a truly fit-for-purpose solution.
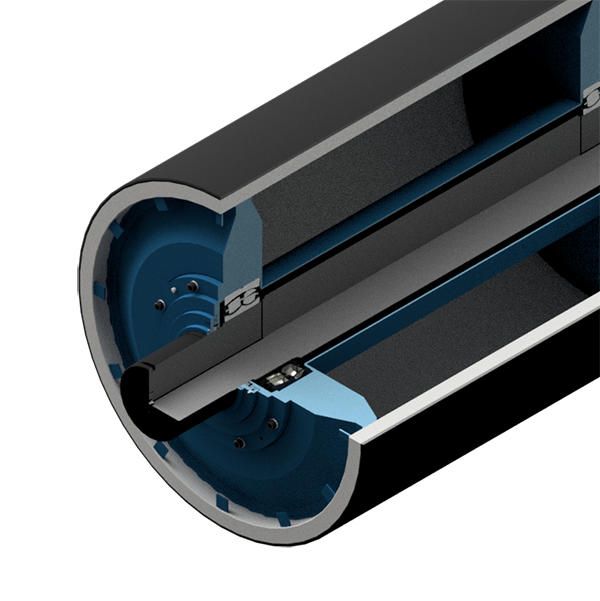
Deadshaft Pulleys
Designed to provide performance in limited space applications including underground environments, as well as weight reduction in gantry applications. This option is able to reduce overall cost and size in comparison to liveshaft designs.
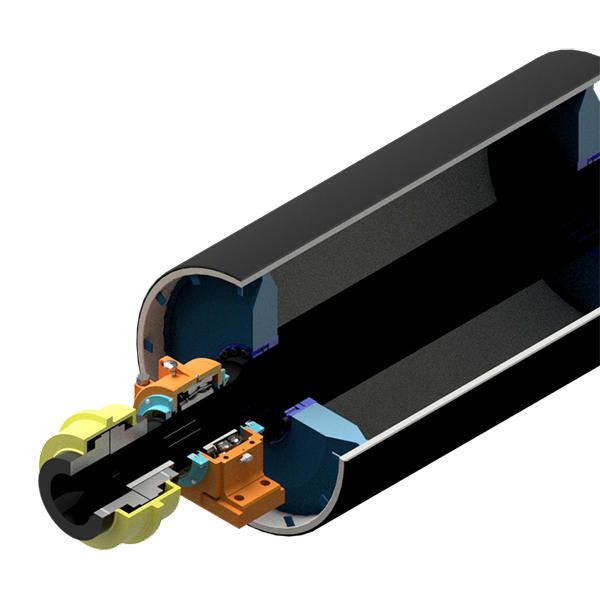
Liveshaft Drive Pulleys
Offered in multiple arrangements depending on drive requirements for the conveyor. Single, dual and braking options available.
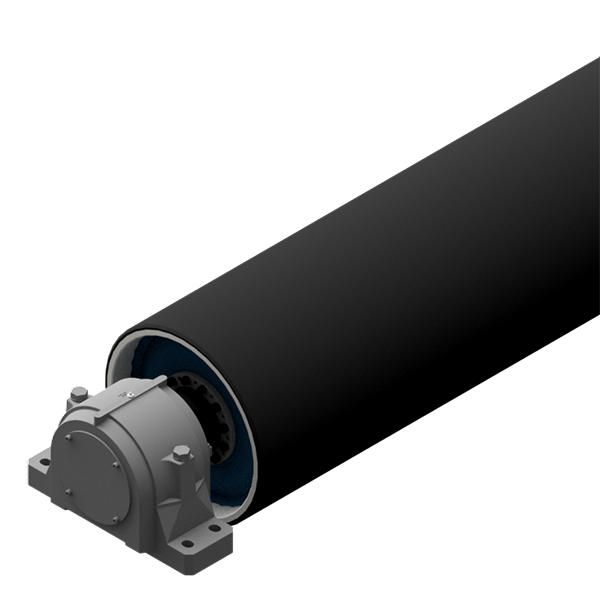
Liveshaft Non-Driven Pulleys
Standard run-of-mine for non-drive applications. Designed to suit both site and application requirements.
We offer an extensive range of customisation options
- Choice of local or international manufacturing location and lead times
- A complete range rubber or ceramic lagging options in FRAS or natural grade and hot or cold vulcanising
- Choice of bearing brand and sealing arrangement
- Service life guarantee
- FEA finite element analysis (recommended on high loaded pulleys)
- A range of testing options including: Ultrasonic Testing, Magnetic Particle, Dye Penetrant and Paint Dry Film Thickness Inspections
Resources
Locally Made & Designed For You
Your choice of bearings, manufacturing location and lead time, lagging, and testing regime are just a few of the cost-saving options we encourage you to consider.
Our list of standard inclusions is all but standard
- Comprehensive manufacturing and testing records, catalogued by individual serial number
- Static balancing
- Pulley bodies thermally stress relieved prior to machining
- All materials meet our stringent internal quality requirements as well as industry standards
In addition to the supply of new pulleys, our Complete Pulley Management service includes:
- Condition monitoring of existing running pulleys
- Management of rotatable spare pulleys
- Ensuring all areas are covered by spares, and changed out pulleys are returned to site fully refurbished, ready for service
Applying the right lagging material is crucial to the performance and life of your conveyor belting and the reliability of your system. As an Original-Equipment-Manufacturer, ACE is able to supply a variety of different lagging options with our own specialist lagging division. We can fit poly, ceramic, rubber and direct bond lagging, and always ensure that our pulley solutions are fit for purpose and best practice supply.
Capabilities:
- Expert customer service personnel to assist you with selecting the best lagging material
- Broad inventory of lagging materials to meet your requirements
- Immediate dispatch of lagging material, including emergency delivery by our own trucks if required
- Safe, expert technicians and factory-trained installers help you minimise downtime and maximise the life of the lagging
Lagging products available:
- Light Duty Natural and Neoprene (food grade) >6 mm
- Natural Rubber Lagging
- FRAS Rubber Lagging (MDA approved for use underground)
- Plain Ceramic Lagging
- Dimpled Ceramic Lagging
- Metal Backed Ceramic Lagging
We also offer a range of on-site conveyor pulley services, including:
- Bearing replacement
- Blasting and re-lagging
- Complete change out and replacement
We also offer off-site Pulley Refurbishment services from our national network of service centres.
After successfully testing hundred of pulleys on our four run-test beds, Fenner ACE has invested the capital into designing a bespoke loaded run machine. This machine is industry leading providing unrivalled adjustability in testing parameters.
During the design phases, nodal analysis was completed to ensure all frequencies of the design were noted and minimised to ensure that no machine vibration is present in the testing.
Finite element analysis is used to determine stresses and deflection in highly loaded pulleys. Third Party SKF testing is completed on all pulleys tested.
Pulley Vibration Testing Capabilities
- Max Pulley Mass - 25,000 kg
- Pulley Diameter - up to 2800mm
- Pulley Bearing Centres - up to 5000mm
- Loading - up to 250kN
- Variable Speed - 0-8m/s
- Adjustable wrap angle to suit pulley application - 10-180 degrees wrap
- Dynamic Balancing on request
Where loaded testing is not required and a more economical option is desired, a standard run-test can be provided with thermal and VA testing, complete with third party report.
Pulley Vibration Testing Capabilities:
- Max Pulley Mass – 12 tonnes
- Max Shaft at Bearing – 360mm
- Shell Diameter Range – 200-1600mm
- Max Bearing Centre – 3000mm
Video available on request
All pulleys are dispatched on certified pulley frame stands. Vibration Analysis and Thermography testing is completed on all newly assembled pulleys. Acceptance testing is also available on long-term stored pulleys prior to installment to provide piece of mind.
Fenner Conveyors provides engineered transport frames including steel skids with custom Working Load Limits and either fixed or jacking mounts, to enable pulleys to be rotated while in their storage cradle.
Ensure your assets are protected from the elements with our additional lagging protection, shrink wrapping and Polyurea/Polyurethane Spray Coating.
Intercept style wrapping is available on all pulleys if required for improved long-term storage. Specialised jacking-style transport frames are available for usage to allow simplified quarterly bearing rotation for pulleys being kept in long term storage.
Peace of mind
At Fenner Conveyors, we don't compromise on quality. All our products are proven in the field and backed by Fenner Conveyors' reputation and warranty. With our nationwide branch network, as well as the support of our Australian Engineering team and manufacturing facilities, you can trust us to be wherever you need us.
Contact us or your local Fenner Conveyors branch for more information.
Related stories
-
Belle Banne’s Latest Belt Puller: 25 Years of Evolution and Innovation
The Belt Puller by Belle Banne is an established piece of equipment that has become indispensable for efficient conveyor belt installs and changeouts. -
Wharf Belt Replacement: A First at Pilbara-Based Port Operation
Collaboration between Fenner Conveyors and a valued Pilbara client has ensured the successful completion of a major wharf conveyor belt replacement. -
Value Up Close and Personal
Fenner Conveyors is offering its customers the opportunity to visit its manufacturing facilities and see how its products are made. -
Belle Banne Belt Handling: Equipment that does the heavy lifting
With the backing of Fenner Conveyors, Belle Banne Belt Handling Equipment is transforming its reach – while staying true to its roots. -
Fenner Conveyors and Rio Tinto renew partnership
Fenner and Rio Tinto renew 5-year deal to supply Australian-made conveyor belts, boosting local jobs, safety, and sustainability. -
Pink and Blue Conveyor Belt Winders in Support of Health Awareness for Roy Hill
Belle Banne delivers pink and blue belt winders to Roy Hill, supporting breast cancer and men’s health awareness initiatives. -
Highest Strength Conveyor Belt Ever Produced from Kwinana
Fenner delivers its strongest conveyor belt ever—ST6300—to a NSW gold mine, custom-built for high-load underground use. -
First Year of K-Mix Construction Complete with 100% Safety Maintained
Fenner marks 1 year of K-Mix plant construction with zero injuries, boosting local jobs, safety, and sustainable manufacturing.
